How to Laser Cut Jewellery: A Guide to Laser Cutting Jewellery, From Adobe Illustrator to Finished Pieces
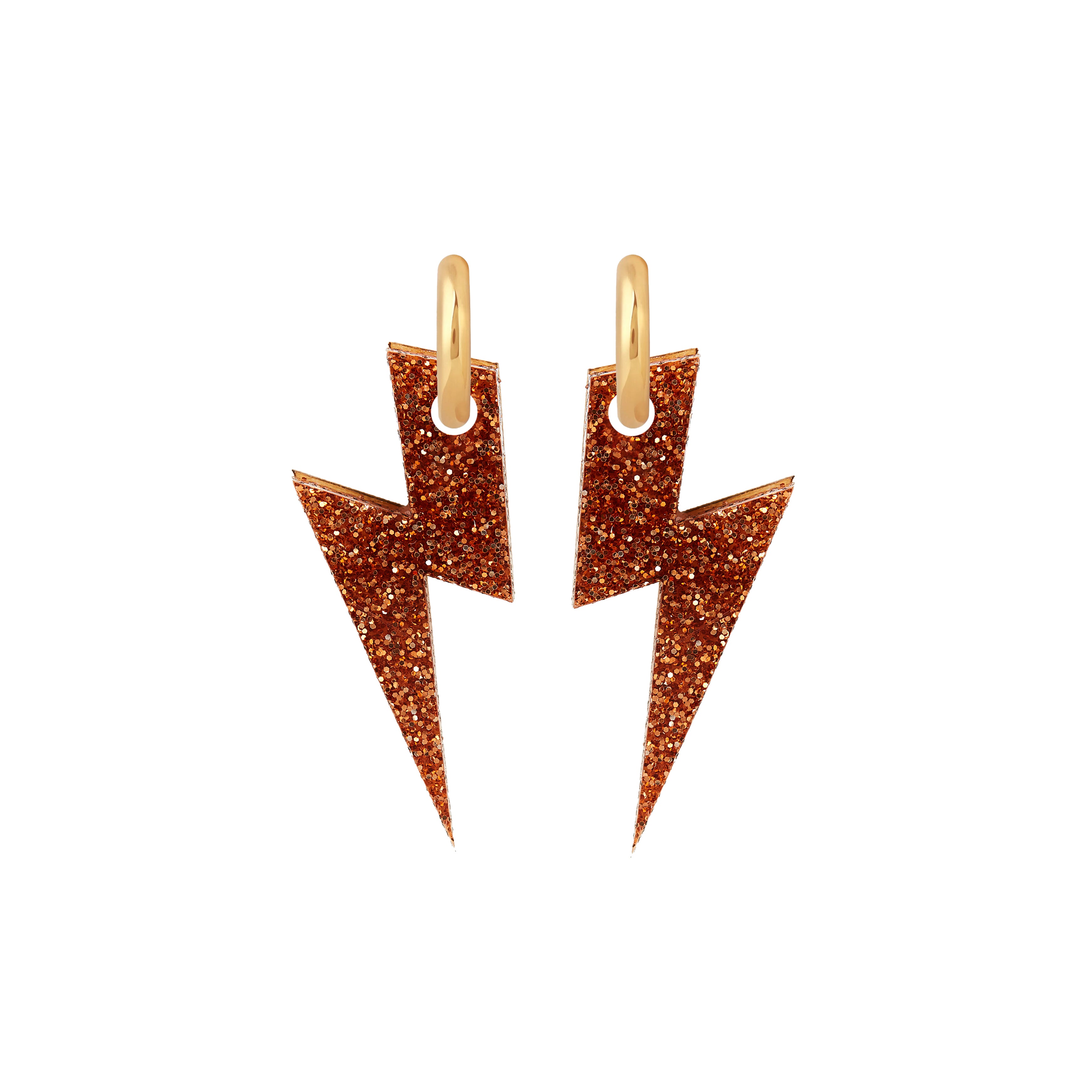
In this guide, I'll take you through the steps of designing your jewellery using Adobe Illustrator, exporting the file, and finally laser cutting your pieces.
This is how I laser cut my jewellery, and how I typically prepare artwork and files. This guide may be useful for those who wish to create files or are wondering how to laser cut jewellery. It will be beneficial too for those who would like to use a laser cutting service, like mine Laser Babes, where i offer a service to cut your laser cut jewellery or your laser cut shapes.
### Tools You'll Need
Before we dive into the process, here’s a quick list of what you'll need:
- **Adobe Illustrator** for creating vector designs
- **Laser cutting software** to manage your design files and settings
- **Laser cutting machine** suited for your chosen materials
- **Materials** like wood, acrylic, or metal, depending on the type of jewellery you want to create
### Step 1: Designing in Adobe Illustrator
The first step in creating laser-cut jewellery is to design your pieces in Adobe Illustrator. Illustrator is a powerful tool that allows you to create highly detailed vector designs, which are ideal for laser cutting. Vector designs are crucial because the laser cutting machine follows paths created by vectors, enabling it to cut with precision.
#### Tips for Designing:
- **Set the right artboard size**: Start by setting your artboard size to match the material size you're working with. This ensures your design will fit the material during the laser cutting process.
- **Use simple shapes**: Remember that the laser cutter works best with clean, continuous lines. Avoid overly complex details unless you’re sure your machine can handle them.
- **Outline your strokes**: Laser cutters don’t always recognise strokes unless they are outlined. In Illustrator, go to *Object* > *Path* > *Outline Stroke* to convert strokes into paths the laser cutter can read.
- **Use appropriate line weights**: Typically, the lines meant for cutting should be around 0.01mm (depending on your machine's settings). Anything thicker might be read as an engraving or scoring line instead of a cut.
- **Closed paths**: Ensure your shapes are closed paths if they are intended to be cut out. Open paths can confuse the laser cutter, leading to incomplete cuts.
### Step 2: Preparing Your File for Laser Cutting
Once your design is complete, you’ll need to export the file in a format that your laser cutting software can understand. Most laser cutters accept **DXF (Drawing Exchange Format)** files, which are compatible with vector-based software like Illustrator.
#### Exporting as a DXF File:
1. **Check your design**: Double-check your design to ensure there are no overlapping lines or open paths that could cause issues during cutting.
2. **Save your file as DXF**: Go to *File* > *Save As*, and select "DXF" as the file format. When saving, choose the appropriate settings for your laser cutter. Some machines may have specific requirements for version compatibility, so check your machine's manual if necessary.
3. **Test scaling**: Make sure your design is saved to scale. The last thing you want is for your design to appear much smaller or larger when imported into your laser cutting software.
### Step 3: Using Your Laser Cutting Software
Now that you have your DXF file, it's time to import it into your laser cutting software. Each laser cutter comes with its own software that manages the process, such as adjusting the power and speed settings for different materials.
#### Steps in the Laser Cutting Software:
- **Import your DXF file**: Open your laser cutting software and import your design. Make sure the file is imported at the correct scale and that the paths are recognised as cuts.
- **Set the parameters**: Depending on your material (wood, acrylic, metal), adjust the laser’s speed, power, and frequency. These settings vary based on the material thickness, so it may take a few test runs to perfect.
- **Power**: Higher power for thicker materials, but too much power can cause burning or melting, especially on acrylic or wood.
- **Speed**: Slower speeds give the laser more time to cut through dense materials, while faster speeds work for thinner or softer materials.
- **Frequency**: Adjust the frequency for smoothness of the cut, particularly for materials like acrylic which can melt or warp with high heat.
- **Preview the job**: Most laser software will allow you to simulate the cutting process before running it on the machine. This is a good opportunity to check for any errors or unexpected results.
### Step 4: The Cutting Process
Once you’re happy with the settings, it’s time to send the design to the laser cutter. Make sure your material is properly secured on the cutting bed. Many laser cutters come with honeycomb beds to reduce material movement and ensure clean cuts.
#### Safety Considerations:
- **Ventilation**: Ensure your workspace is well-ventilated, especially when cutting materials like acrylic, which can produce fumes.
- **Material testing**: Always test a small section of your material before cutting the entire design to ensure the settings are right and that there’s no excessive scorching.
#### Monitoring the Cut:
- Stay close by while the machine is cutting to monitor the process. Different materials behave differently under the laser, and it’s best to be prepared in case something needs adjustment mid-way.
### Step 5: Finishing Touches
Once the laser has finished cutting, carefully remove your pieces from the machine. Depending on the material, there may be some post-processing involved:
- ** Cleaning up edges**: For materials like wood or acrylic, you may need to clean off any scorch marks or residue. A light sanding for wood or using an acrylic cleaner for plastic can help improve the final look.
- **Assembly**: If your jewellery design involves multiple pieces, now’s the time to assemble them. Attach any findings like earring hooks, chains, or clasps to complete your pieces. This part may involve gluing, which i will cover in a separate post.
Whether you're working with acrylic, wood, or even metal, the possibilities are truly endless. Don’t be afraid to experiment with different materials, designs, and laser settings to find what works best for your style. Happy creating!
laser cut jewellery ideas, laser cut jewellery uk, laser cut jewellery stand, laser cut jewellery box, laser cut jewellery, laser cut jewellery uk, how to laser cut jewellery, can you laser cut jewellery, laser cut acrylic shapes for jewellery
Comments